Case Study - How Lime Associates sourced China supply chain for global Medical Technology business
21st April 2013
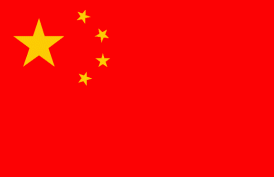
Our Client: Our client, a leading global Medical Technology business with a presence in over 90 countries and employs over 10,000 people worldwide.
Project: The client recognised that it could reduce its cost of manufacture by building a factory in China but was also mindful of the potential risks associated with such a venture. The plant would be a long way from its customers in Western Europe and North America and not only would there be freight cost implications, but the long lead times would impact on cash tied up in inventory.
Actions: The actions were threefold. Firstly, Lime Associates used its lean manufacturing expertise to ensure that the products were planned to be manufactured promptly to customer requirements to reduce time in the factory and help to offset extended freight time. Secondly, Lime Associates managed the business team designing SAP enabled processes to ensure that lean manufacturing was thoroughly embedded in the factory’s systems and ways of working and thirdly, the team managed a freight RFQ and negotiated the best ocean container freight rates, terms and lead times to the client’s chosen destinations.
Result: Lime Associates secured distribution savings of $1 million with no increase in stockholding and storage costs by shipping direct to regional distribution centres.
Summary: Lime Associates used its cross functional Medical Industry supply chain and procurement experience to satisfy the client’s brief and deliver exceptional savings in the time frame allocated.
To find out more about how we can help you or to ask any questions, please feel free to contact us on 0114 213 8306, enquiries@lime-associates.com or
www.lime-associates.com
Categories: Case Studies, Supply Chain Management, Health Technology, Medical Device
Archives
- 2017
- 2015
- 2014
- December
- November
- October
- August
- July
- June
- May
- April
- March
- East Riding businessman invited to address national conference
- New group launched to address supply chain challenges facing medical companies
- How ethical is your procurement and supply?
- Case Study – Travel procurement project highlights over £660k savings per annum
- Case Study – An ERP project for multi-million pound medical company
- February
- January
- 2013
- December
- November
- Sheffield medical technology consultants help Oxfordshire Medical Device manufacture to choose ERP System
- High praise for Lime Associates’ James Cooper at national med-tech conference
- November newsletter
- Tri-partite event unites medical purchasing and supply chain professionals
- Representing the client - the importance of trust in third party relationships
- October
- September
- August
- July
- June
- May
- April
- March
- February
- January
- 2012
- December
- November
- October
- September
- July
- June
- May
- April
- March
- Case Study - World carton board market interrogated to identify sourcing opportunities
- "Time well spent" - CIPS Health Technology Group Launch event
- CIPS Health Technology Launch Event
- Purchasing and sales - best of friends?
- Top 10 Tips for your next CIPS awards
- Specialist Health Technology Consultancy celebrates second successful year
- Lime Associates' Chairman on the Radio
- James Cooper's in the news
- One is the magic number for Lime Associates' Chairman
- New group attracts both global giants and SMEs
- Lime Associates negotiates hard to deliver recruitment savings
- New Group Launched to address purchasing and supply changes facing medical companies
- CIPS Health Technology Group Speaker Biographies
Categories
- Case Studies
- Media
- CIPS Professional Group
- Cost Control
- Cost Reduction
- Supply Chain Management
- Training
- Consultancy
- Health Technology
- Medical Device
- Bio-Tech
- Start Ups
- Lime In The News
- iCEO
Newsletter Sign Up
Enter your email address below to subscribe to our newsletter.